品質管理における基本工程と
「測定器の役割」とは?
品質管理における3つの工程
製造業における品質管理は、その製品の安全性・機能性を担保するうえで非常に重要なプロセスです。特に、自動車部品や医療機器などの場合、製品の品質が人命に影響を与えるケースも考えられるため、より一層厳しくチェックが行われます。
製品・材料の品質が定められた規格・基準などの要件を満たしているかどうか、チェックするために行われるのが「検査」です。検査は主に以下3つの工程が存在します。
受入検査
受入検査は、材料や購入品が自社の品質基準を満たしているかを確認する最初の工程です。この工程では、供給された材料や部品の規格や寸法の元図面との整合性、外観の傷や打痕がないかをチェックします。
外注加工品の場合は、材質や熱処理が指定通りに行われているかを確認するために、サプライヤーから提供される材料証明書(ミルシート)や各種証明書を取得し、それらを照合して保管します。
後続の検査工程(工程内検査や出荷前検査)で問題が発覚した場合、まずはこの受入検査で確認済みだったかどうかの確認が行われます。迅速な原因追及と対応を行ううえでも、最初の受入検査は重要があります。
受入検査については下記の記事もご覧ください。
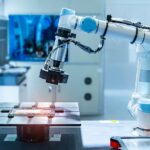
受入検査とは? 目的・基準を紹介
工程内検査
工程内検査は、製造プロセスの各段階で行われる検査で、製品が設計通りに製造されているかを確認する工程です。この検査は、加工工程ごとに行われる場合もあれば、製造ラインの中でオペレーターが直接行う場合もあります。精密な寸法検査や外観検査を通じて品質基準を満たしていることを確認し、結果は「工程内検査表」や「工程管理表」に記録されます。
工程内検査の記録は製品の品質履歴を管理しているものなので、万が一問題が発生した場合にどの段階で異常が発生したかを特定するために用いられます。工程内検査は不良品の大量発生を防ぎ、製品の品質を一貫して高く保つために重要な工程です。
出荷前検査
出荷前検査は、製品が完成した後に行われる最終検査で、製品が顧客に納品される前に行われます。この工程では、各種測定器具を使用して製品の寸法や形状が設計図面の指示通りであるか、また外観に問題がないかを厳密に確認します。
検査結果は「検査表」などに記録され、品質記録として保管されるだけでなく、必要に応じて顧客に提出されることもあります。万が一、出荷前検査で不良が発見された場合には追加工や修正が行われ、顧客に最良の製品が届けられるよう対応します。また、使用する測定器具は定期的に校正され、その校正証明書も品質記録として保管されます。
出荷前検査は、顧客に届ける製品の品質を担保するための最終的な砦であり、顧客満足度や企業への信頼度を維持するための重要な工程です。
出荷検査に関しては以下の記事もご覧ください。
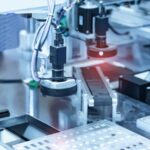
主な検査項目・測定器具
では、実際に各検査工程ではどのような検査項目が設けられるのでしょうか。
前章でも一部ご紹介しましたが、主な検査項目としては「寸法検査」「外観検査」の2つがあります。それぞれの検査内容と、用いられる測定器具は以下の通りです。
寸法検査
寸法検査は、製品の各部品が設計通りの寸法で製造されているかを確認するための検査です。一般的な寸法測定器具として、マイクロメータ、ノギス、3次元測定機(CMM)などが使用されます。
外観検査
外観検査は、製品の外観にキズや汚れ、変形がないかを確認する検査です。一般的な方法としては、目視検査や画像処理技術を用いた検査が行われ、製品の外観に問題がないかの確認を行います。
品質管理における測定器の役割
品質管理という面において、測定器が持つ役割をまとめると大きく3つが挙げられます。以下、それぞれについてご紹介します。
検査基準を満たすかのチェック
1つ目は、製品が設計仕様や顧客要求に適合しているかを確認する役割です。寸法などが定められた規格や基準内(例:測定誤差の範囲内か)に収まっているかどうか確認をし、品質を担保する役割です。
品質記録(データとトレーサビリティ)
2つ目は、「品質」という概念を数値化して定量的データとして記録することです。測定器を使用して取得したデータは、品質管理のための書類やシステムに記録されて、課題の分析や問題の追跡などに役立てられます。品質向上のための具体的な対策を講じることができるのも、測定器で品質を数値化して記録しているからこそ行えるといえるでしょう。
人が目盛りを読んでアナログに記録を行わなうことをせず、システム的に自動記録した後、それらのデータを様々な分析に役立てるようにします。
品質問題の未然防止と製造工程改善支援
3つ目は、問題を早期発見してトラブルを未然防止することです。
測定器を使用した検査は、製造プロセス中に発生する可能性のある品質問題を早期に検出して不良品の流出を防ぐなど、その後の顧客クレームや損失といったリスクを抑えることにも繋がっています。そして、それ等の不良品データが、製品設計や製造プロセスの改善策を示唆する重要なデータとなります。
高精度・効率的な角度検査ならオートコリメータ
品質検査をおこなう上で、検査対象の角度測定を行うシーンもあるかと思います。
角度の測定を、高精度かつ迅速に行いたい場合は、ピック・ゲージや分度器などを用いたアナログな角度測定方法ではなく、オートコリメータの使用がおすすめです。
オートコリメータとは、測定にレーザーを用いた角度測定機器で、光学原理を用いて測定をおこなう方式のため小数点以下の細かい角度測定を簡単に行うことができ、従来の分度器などの器具を用いた測定方法と比べて高い精度での測定が可能です。
更に、レーザー光を用いて測定対象に非接触で測定ができるので測定対象を傷つける心配がなく、また複数箇所の測定をする場合でも一度に測定結果を求めることができるため、角度測定にかかる時間を大幅に短縮できるというメリットもあります。
弊社では、高精度なレーザオートコリメータ 「Smart LAC」をご提供しています。
Smart LACは、さまざまなモデルや機能を選択でき用途や要件に合った最適なオートコリメータを選ぶことが可能です。注文から1週間で納品が可能ですので、お急ぎの場合もご相談ください。
Smart LACの詳細な製品情報を知りたい方は、下記の資料をご覧ください。
製品資料
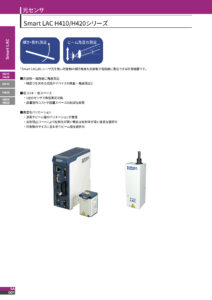